3 min read
How Manufacturers can become Industry 4.0 and IIoT Ready?
Anurag : Jan 4, 2018 10:00:00 PM
Industry 4.0 is the current stage of the industrial revolution. It represents the use of Industrial Internet of Things (IIoT), automation, sensor technology and other innovative solutions to streamline the production and distribution.
The Industry 4.0 brings in the concept of “smart factory”. It focuses on the use of cyber-physical systems to monitor the physical factory processes and make data-based automated decisions. While the physical systems are made the intelligent using Internet of Things, the real-time communication, and cooperation both with each other and with humans is established via the wireless web.
Interested in Manufacturing IoT? Catch the latest updates, strategies and innovations with our free ebook. Download now.
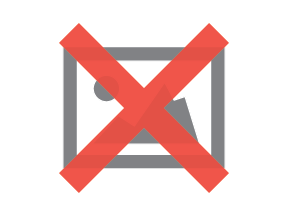
Feel free to use this image. Just give us a mention.
IIoT forms the backbone of any initiative towards achieving Industry 4.0. By using sensor technology IIoT enables transmission of signals from machinery to computer systems. While basic information about machinery has been accessible for quite a bit of time, IIoT brings in much more sophisticated insights about business. This micro-specific information provides scope for automation. If analyzed properly, the data received from IoT sensors can provide insights to optimize various aspects of the manufacturing process.
Read More: 8 Applications and Benefits of IIoT
What Makes a Factory an Industry 4.0 Ready?
These are the 4 prerequisites for a factory or system to be considered Industry 4.0:
1. Interoperability:
The lines of communication should be established as such that it defines a clear method on the exchange, use, and collection of data. Different machines, devices, sensors and people should be able to share information and act on the data received.
2. Information transparency:
It is important that the information received is clear, concise and understandable. Logs from sensors make it tough to take action due to difficulty in comprehension. To solve this, the systems should create a virtual copy of the physical factory architecture using sensor data to contextualize information.
3. Technical assistance:
The system should help a human in two ways. Firstly, it should support us in decision making and problem-solving by providing insights based on data. Secondly, it should assist in tasks that are difficult or unsafe to be performed directly by humans.
4. Decentralized decision-making:
The cyber-physical systems should be capable of making simple decisions using data analysis. The ultimate aim of Industry 4.0 is to automate the factory process to the maximum extent possible. Using robotic process automation manual routine work can be undertaken by machines offering an increased scope for optimization of time and resource allocation.
Read More: Impact of Cloud Computing in Manufacturing
Challenges Involved in Implementing Industry 4.0:
Every radical shift in business comes with some challenges. So is the case with Industry 4.0. While implementing Industry 4.0 following challenges might come in your way:
1. Security Issues:
The entire data is made available via the internet to remote devices. This exposes critical data to the risk of security breach, data theft, and manipulation. The proprietary production knowledge if accessed by a hacker can result in massive damage to company’s revenues.
2. Reliability and Stability:
If the communication received via IIoT sensors is unorganized or untimely then it is impractical to consider it reliable. Obviously, you cannot automate a factory functioning based on unreliable or unstable data. It is complicated to maintain the integrity of production process while minimizing the need for human interference.
3. Establishing Connectivity:
It is nearly impossible to ensure 100% internet connectivity. Even if the network is not likely to go down unexpectedly, you will need to account for maintenance of servers. It is challenging to ensure 0 data loss even in case of extreme connectivity issues or sudden outbreaks.
4. Blending Legacy Systems with IIoT:
Legacy systems weren’t designed to comply with the requirements of sensor technologies. But modernizing the entire infrastructure isn’t feasible for most manufacturers. Hence, it is required to blend modern IIoT technology with the legacy machinery to ensure the best ROI on manufacturer’s investment.
Apart from the above challenges, manufacturers also face issues from investors and in-house technical team. Investors are quite reluctant to large-scale revolutions. At the same time, the available IT talent isn’t usually updated to handle such challenges. Market research data and trends towards digital transformation have opened the eyes of investors. Limited technical capabilities still remain a common concern while performing any IIoT implementing.
This is where NewGenApps can help. Over the period of 10 years, we have developed specialized skills in working on innovative solutions. We have a highly skilled team of developers who can develop scalable IoT applications in any field. Contact us today for a project or POC.
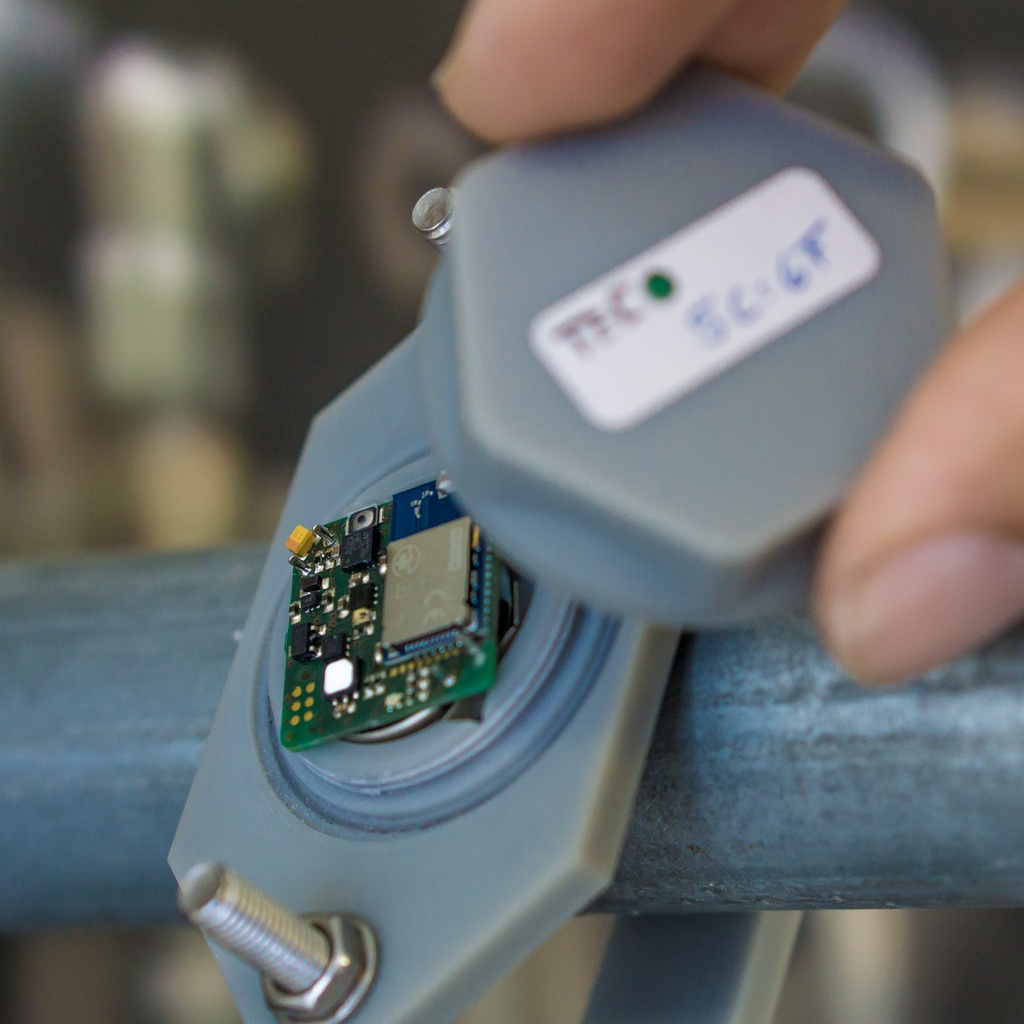
1 min read
How IoT has altered the manufacturing industry
The working environment is changing and so is the strategies and how things are conducted within and outside the organizations. Trends are...
1 min read
Industrial IoT (IIoT) Implementation: 8 Places You Can'T Go Wrong
One of the most widespread developments in the industrial world has been the introduction of the Internet of Things (IoT) over the past decade, which...